WATER TREATMENT PLANT
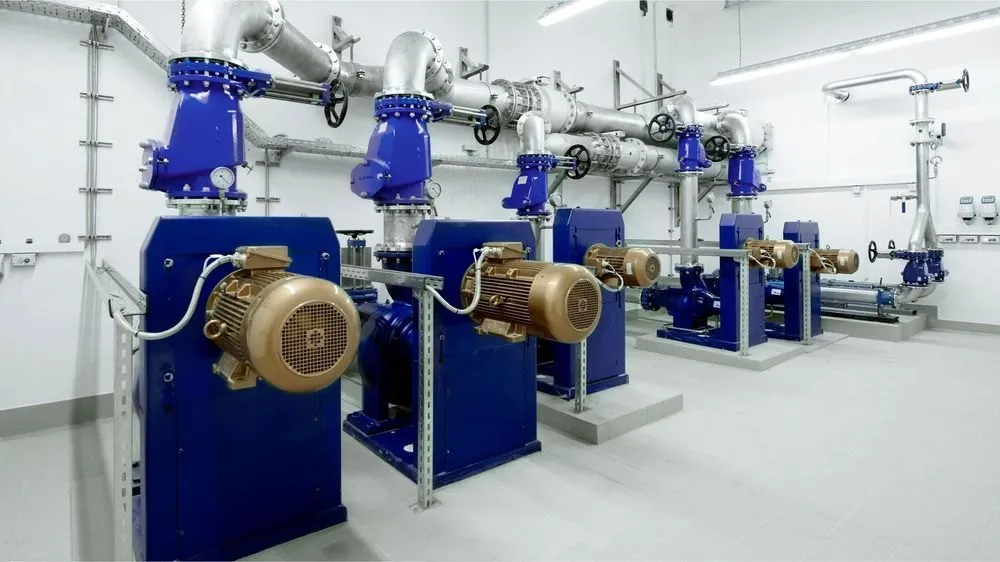

A fully automated water treatment plant refers to a facility that treats water for consumption, industrial use, or other purposes through automated processes. The goal is to purify water by removing contaminants such as bacteria, viruses, sediments, and chemical pollutants while ensuring efficiency, safety, and minimal human intervention.
Water Intake and Screening
- Raw Water Source: Water is drawn from a natural water source such as a river, lake, reservoir, or groundwater well.
- Automated Intake System: Sensors and control systems regulate the water intake to ensure the right flow rates.
- Pre-Screening: The first stage of treatment involves physical barriers or automated mesh screens to remove large debris like leaves, branches, and plastic. This process helps prevent damage to pumps and equipment.
- Automated Flow Regulation: Flow meters and control valves adjust the water intake based on demand and available water.
Coagulation and Flocculation
- Chemical Addition: Automated systems add coagulants (such as aluminum sulfate) to the raw water to neutralize the charge of particles suspended in water. This process clumps these particles into larger aggregates called flocs.
- Flocculation Process: Water is slowly stirred using automated mechanical mixers or flocculators. The stirring helps the tiny particles bond into larger clusters.
- Automated Chemical Dosing: The correct amount of coagulant is dosed based on real-time water quality data, ensuring optimal performance and minimal chemical waste.
Sedimentation
- Clarification Tanks: The water flows into a large sedimentation basin or clarifier. In this basin, the heavier flocs settle to the bottom due to gravity.
- Automated Monitoring: Sensors detect the water’s turbidity (cloudiness) and the settling rate of flocs. Automated systems control the speed and duration of the water flow to maximize sedimentation efficiency.
- Sludge Removal: The accumulated sludge (settled particles) is periodically removed by automated scraper systems at the bottom of the tank.
Filtration
- Filtration Units: After sedimentation, the water still contains finer particles and microorganisms. It is passed through filters that remove these impurities.
- Types of Filters:
- Sand Filters: Remove suspended solids.
- Activated Carbon Filters: Remove organic compounds and chlorine.
- Membrane Filtration (e.g., Reverse Osmosis): Removes dissolved salts and microorganisms.
- Automated Backwashing: When the filters become clogged, automated backwashing systems reverse the flow of water to clean and restore filter capacity.
- Online Monitoring: Sensors measure the pressure difference across the filters, triggering automated backwashing when necessary.
Disinfection
- Chlorination / UV Treatment: To ensure microbial safety, the water is disinfected through automated dosing of disinfectants (like chlorine) or by using ultraviolet (UV) light.
- Automated Disinfection Control: The amount of disinfectant is adjusted in real time based on parameters such as water flow rate, chlorine residual, and UV intensity, ensuring effective disinfection without over- or under-dosing.
- Ozonation (in some plants): Ozone gas is injected into the water as a strong disinfectant, with automated ozone generation systems.
pH Adjustment and Final Treatment
- pH Control: Automated systems monitor the pH levels of the water. If necessary, chemicals like lime or sodium hydroxide are added to adjust the pH to a safe and acceptable range.
- Final Polishing: Additional treatments (like activated carbon or final filtration) may be used for polishing the water to ensure all contaminants are removed.
Storage and Distribution
- Storage Tanks: The treated water is stored in reservoirs or tanks. Sensors continuously monitor the water levels, and pumps are controlled to maintain a constant supply.
- Automated Distribution: The water is then distributed through a network of pipes to consumers. Flow sensors, pressure sensors, and automated valves ensure an even and adequate distribution while preventing issues like pipe bursts or low pressure.
- Remote Monitoring: Operators can monitor the status of the plant and distribution system remotely, often through a Supervisory Control and Data Acquisition (SCADA) system.
Wastewater Treatment and Sludge Management
- Sludge Handling: The sludge from sedimentation and filtration processes is treated using automated systems for thickening, dewatering, and disposal.
- Wastewater Treatment: Some plants also handle the treatment of wastewater (from households or industries). Automated systems control the aeration, filtration, and disinfection stages in wastewater plants.
- Sludge Incineration or Landfilling: In some cases, treated sludge may be incinerated or transported to a landfill.
Control Systems and Automation
- SCADA (Supervisory Control and Data Acquisition): The heart of a fully automated water treatment plant, SCADA systems collect real-time data from sensors throughout the plant (flow rates, turbidity, pressure, chemical levels) and control the equipment remotely.
- Predictive Maintenance: Automated systems can predict potential failures based on trends and data from sensors, allowing for preventive maintenance.
- Data Analytics: Continuous data collection allows for ongoing optimization of treatment processes, improving energy efficiency, reducing chemical usage, and enhancing water quality.
Remote Monitoring and Management
- Data Transmission: The entire system can be monitored in real time from a central control room or even remotely via the cloud, where operators can access critical data and adjust settings.
- Automated Alerts: If any parameter goes out of the desired range, automated alarms and alerts are triggered to inform operators about potential issues.
Benefits of Fully Automated Water Treatment Plants:
- Reduced Human Error: Automation reduces the chance of mistakes made by operators.
- Energy and Chemical Efficiency: Automation optimizes the use of energy and chemicals based on real-time data, reducing costs.
- Continuous Monitoring: Sensors monitor water quality 24/7, ensuring that the water is always treated effectively.
- Faster Response Time: Automated systems can react quickly to any changes or issues, such as equipment failure or changes in raw water quality.
- Improved Safety: Minimizes the need for manual intervention in hazardous areas, such as chemical dosing or working with pressurized systems.
- Data-Driven Decisions: The system collects vast amounts of data, which can be analyzed for process improvements and regulatory compliance.
Conclusion:
A fully automated water treatment plant uses advanced technologies and control systems to efficiently treat water while minimizing human intervention. The integration of sensors, automated chemical dosing, filtration, disinfection, and remote monitoring ensures that the water treatment process is consistent, reliable, and cost-effective. It offers numerous benefits such as improved water quality, efficiency, and safety for both the environment and the plant operators.